Paver Block Manufacturing Process
Paver blocks have gained popularity in contemporary building due to their robustness, longevity, and versatility in design. These precast concrete elements are widely employed in the construction of driveways, walkways, patios, and various outdoor areas. This blog will explore the characteristics and production process of paver blocks, as well as the benefits of utilizing a Polycarboxylate (PC) based hardener instead of the conventional calcium chloride hardener.
Table of Contents
1) What is a Paver Block?
Paver blocks, also referred to as paving stones, are precast concrete elements utilized for building solid outdoor surfaces. They are valued for their long-lasting nature, simple installation, and capacity to form complex patterns. Paver blocks come in different forms, dimensions, and shades, offering flexibility in landscaping and architectural plans. Moreover, their interlocking structure ensures adaptability, enabling effortless repairs and modifications.
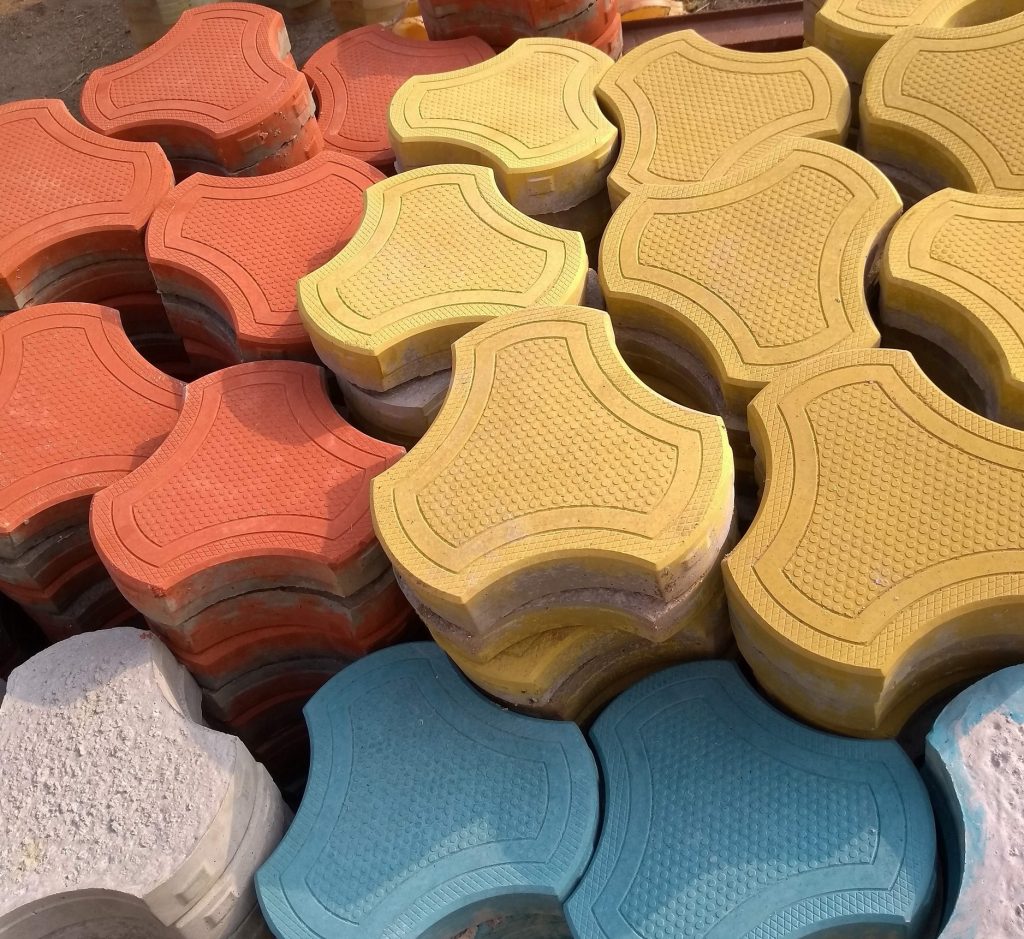
2) How to Manufacture Paver Blocks – Paver Block Manufacturing Process
To produce paver blocks with ideal strength and appearance, it is crucial to have an accurate mix design and appropriate additives. The manufacturing procedure entails the creation of two distinct layers: the color layer on top and the structural layer at the back. We will now provide details on the mix design for each layer and highlight the advantages of utilizing a PC-based hardener.
a) Mix Design for the Top/Color Layer (M20)
The top layer of the paver block, which is visible and exposed to traffic, requires a mix design that offers both strength and a smooth finish. An M20 mix, which has a compressive strength of 20 MPa, is ideal for this layer.
- Mix Ratio: 1 part cement : 1.5 parts sand : 3 parts aggregates
- Additives: High-quality pigments, such as Iron Oxide, are added to achieve the desired color.
- Water-Cement Ratio: Maintain a water-cement ratio of around 0.4 to 0.45 for the right consistency and strength.
b) Mix Design for the Back Layer (M10)
The back layer provides the structural integrity of the paver block. An M10 mix, with a compressive strength of 10 MPa, is suitable for this purpose.
- Mix Ratio: 1 part cement : 3 parts sand : 6 parts aggregates
- Water-Cement Ratio: Keep the water-cement ratio at around 0.5 to ensure proper compaction and strength.
c) Using PC-Based Hardener for Best Results
To enhance the quality and performance of paver blocks, a Polycarboxylate (PC) based hardener is highly recommended. This hardener improves the workability of the concrete mix, leading to better compaction and a superior surface finish.
d) Advantages of PC-Based Hardener over Calcium Chloride Hardener
- Cleaner Molds: PC-based hardeners prevent the concrete mix from sticking to the molds, resulting in cleaner molds after demolding. This reduces or even eliminates the need for manual cleaning, which can save time and extend the lifespan of the molds.
- Extended Life of PVC Molds: Unlike calcium chloride, which generates heat during the hydration process and can degrade PVC molds, PC-based hardeners do not cause the concrete to heat up as much. This helps in preserving the integrity and longevity of PVC molds.
- Reduced Iron Oxide Requirement: The use of a PC-based hardener can reduce the amount of Iron Oxide needed in the color layer, enabling the desired color with less pigment. This leads to cost savings and more efficient production.
- Cement Savings: With a PC-based hardener, cement usage can be reduced by up to 10-20% without compromising the strength or durability of the paver blocks. This not only makes the production process more cost-effective but also more environmentally friendly.
Conclusion
Paver blocks are an excellent choice for a variety of outdoor applications due to their durability, aesthetic appeal, and versatility. By following the appropriate mix designs for the top and back layers, and by using a PC-based hardener, you can produce paver blocks that are not only strong and durable but also cost-effective and visually appealing. The advantages of PC-based hardeners, such as cleaner molds, extended mold life, reduced Iron Oxide requirements, and cement savings, make them a superior choice over traditional calcium chloride hardeners. #Paver Block Manufacturing Process
See our Trigonometry Formulas